Infrastructure
Our Facility
DESIGN AND ENGINEERING
Windlass has a long and successful track record of innovative quality design engineering solutions for components and assemblies. Our philosophy is to fully and clearly understand the requirements of our customers and to reflect this in appropriate design solutions. We encourage innovation in design and all our engineers keep abreast of rapidly evolving technology and techniques. We use latest Solidworks software for designing and simulation. Windlass Design team provides customer with independent support at every stage of a project from designing, testing and operation.
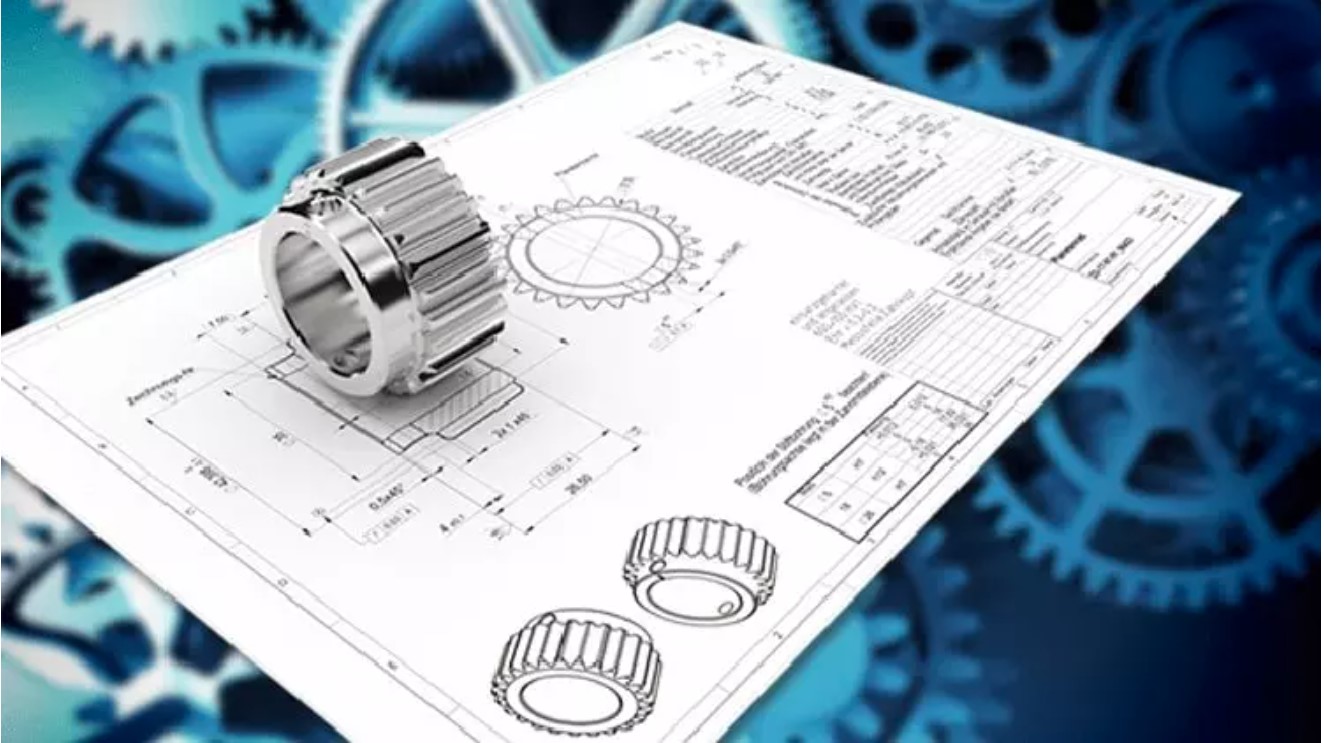
Our Machines
MACHINING
To provide quality machining to the customer’s satisfaction has always been top priority of Windlass. We are capable of producing precision machining parts, assemblies as well as tooling and fixtures. We are fully qualified and have countless hours of experience in performing a variety of machining tasks, including:
- CNC Machining
- CNC CADCAM Milling and Turning
- General Machining
- 3,4 and 5 AXIS Milling
- Machining up to 1200 mm diameter and 3 meter long shaft
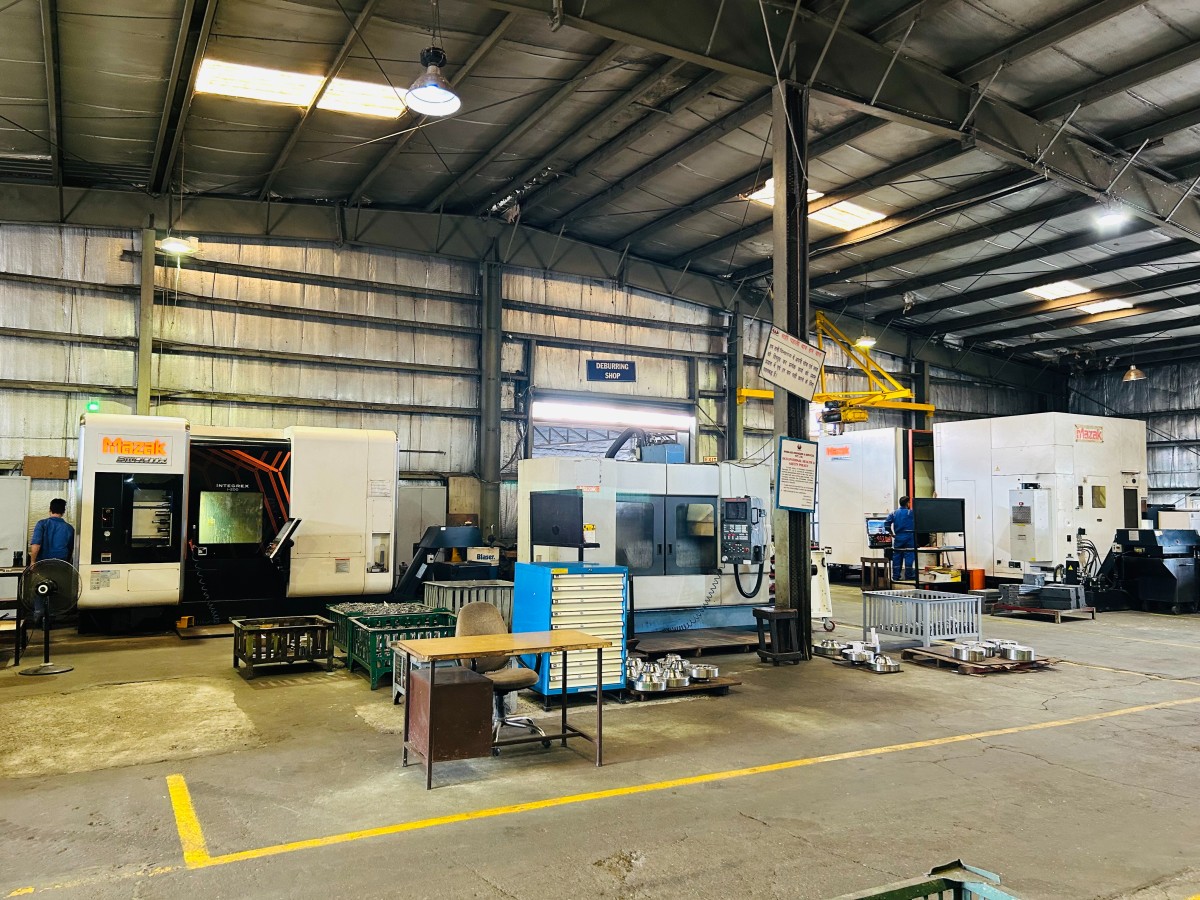
- Mazak Integrex 5 axis CNC Machine
- Mazak Turn-Mill CNC Machine
- CNC Horizontal Turning Centers
- CNC Vertical Turning Centers
- CNC Vertical Milling 3,4 and 5 axis Machines
- CNC Horizontal Milling Machine
- Solid CAM Software for complex machining
- General Lathes
- Milling Machines
- Radial Drill Machines
- Vertical Boring Machines
- Plano Miller Machine
- Grinding Machines
- Lapping Machines
- Band Saw Machines
CLOSED DIE FORGING
Windlass produces forgings in a variety of sizes and configurations to meet customer requirements
- 2 Tons Hydraulic Closed Die Hammer capable to produce up to 20 Kg piece
- 300 Tons trimming and punching press.
- Backup power to support forging operations
- 3 Ton Belt drop Hammer capable to produce up to 60 Kg piece
- 500 Tons trimming and punching press.
- Induction Furnace 350 KVA
OPEN FORGING
- Pneumatic Open Forging Hammer capable to forge 5 Tons single piece forging
- High Speed Bend Saw Machines capable to cut up to 1100 mm dia ingot.300 Tons trimming and punching press.
- 3 Ton Belt drop HamTemperature controlled furnaces for forgingsmer capable to produce up to 60 Kg piece
- 5 tons and 10 Tons overhead cranes.500 Tons trimming and punching press.
- 950 CFM Air compressor with 18000 liters air receivers.
HEAT TREATMENT
- Electrically Operated Hardening and Tempering Furnaces
- Heat Treatment process monitored and recorded by SCADA software
- Oil, Water and Polymer Quenching facility
GAS NITRIDING
- Surface hardness up to 65 HRC and case depth upto 800 microns can be achieved depending on the material grade
BORONIZING
- Electrically OperateHigh micro surface hardness up to 2000 HV on steel alloys and upto 2800 HV on nickel based alloys can be achieved Hardening and Tempering Furnaces
CARBURIZING
- Surface hardness upto 60HRC and case depth more than 500 microns can be achieved
FABRICATION
We offer customised metal fabrication for all industrial applications specially design to meet your needs. No fabrication job is too big or too complex for our team of dedicated professionals.
- MIG, TIG and SMAW
- ASME qualified welders
- AWS Certified Inspector
QUALITY CONTROL
A team of Engineers having vast experience in Oil & Gas equipment manufacturing takes care of Quality control services.
- PR-2 Testing Facility
- Universal Testing Machine (UTM)
- Charpy Impact Testing Machine (ASTM)
- Chemical Test Machine (Spectro)cal Turning Centers
- Coordinate Measuring Machine for reverse Engineering and critical dimensional checking.
- Hydro Testing Facility up to 30000 PSI with chart recording.
- Temperature Control Room for Calibration & Master Gauges.
- ACME thread gauges for all ranges of hammer Unions from Hemco Gauges-USA.
- LPT gauges from Hemco Gauges- USA.
- Rubber Hardness Tester
- Brinell Hardness Tester, Model B3000(O)
- Rockwell Hardness Tester Model 'RAS' make 'SAROJ'
- Complete facilities for Magnetic particle testing with ASNT Level-II certified inspectors.
- Dye penetration testing ASNT Level-II certified inspectors.achines
- Stress relieving facility including Temperature Recorder, Temperature Controller etc.
- Liaison with third party for Radiography
- Special Purpose BX1000 and BXG1000 gauges of GAGEMAKER-USA for measuring of Ring Grooves
- Ultrasonic thickness tester
- Ultrasonic Flaw Detector
PRESSURE TESTING
- Pneumatic Open Hydrostatic Pressure Testing upto 30,000 PSIForging Hammer capable to forge 5 Tons single piece forging
- Gas Testing up to 15,000 PSI
- Temperature from -60 degree C to 121 degree C for cyclic test
- PR-2 Pressure teting validation
- 5 tons and 10 TonTesting cycles recorded on Chartss overhead cranes.500 Tons trimming and punching press.
OTHER INHOUSE FACILITIES
- NDT Testing
- Water Jet Cutting
- Magnetic Particle, Ultrasonic, Dye Penetrant & Visual
- Shot Blasting
- Powder Coating
- Painting
- Plating plant
- Inspection by ASNT Level ii Inspectors
- Investment and Sand Casting
- Conventional Machining
- Spectrograph Analysis
- In-house Corrugated Box manufacturing